企画・開発から製造、お客様のもとに届くまで。
業界を牽引するメーカーとして、
各分野のプロフェッショナルたちが
「安全・安心」と「革新」という
共通の志をもって働いています。
長谷川工業の仕事 WORK
協力しあって「いいモノ」を送り出す各部署の仕事内容とは?
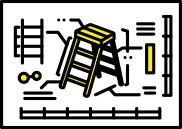

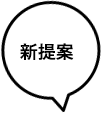
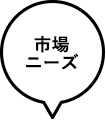
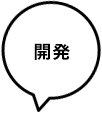

連携しフォローする
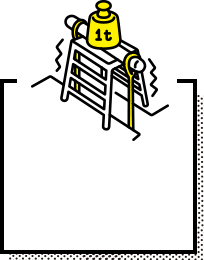
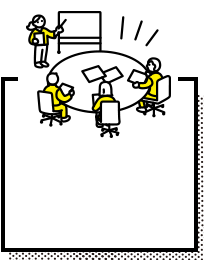
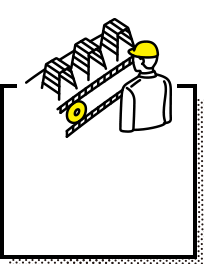
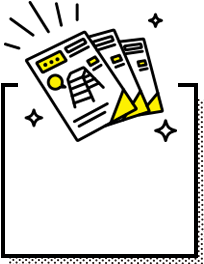
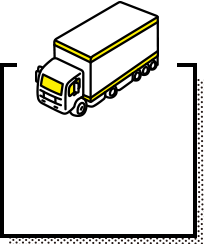
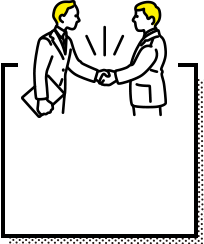
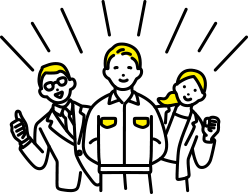
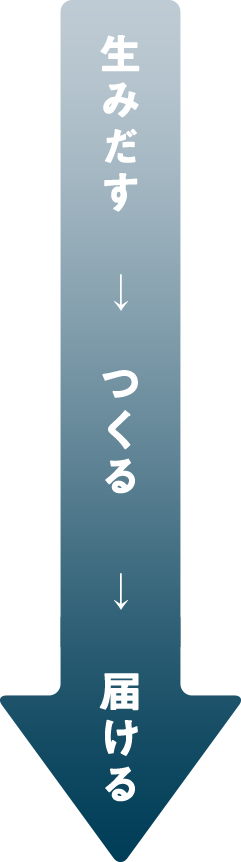
プロジェクト事例 PROJECT
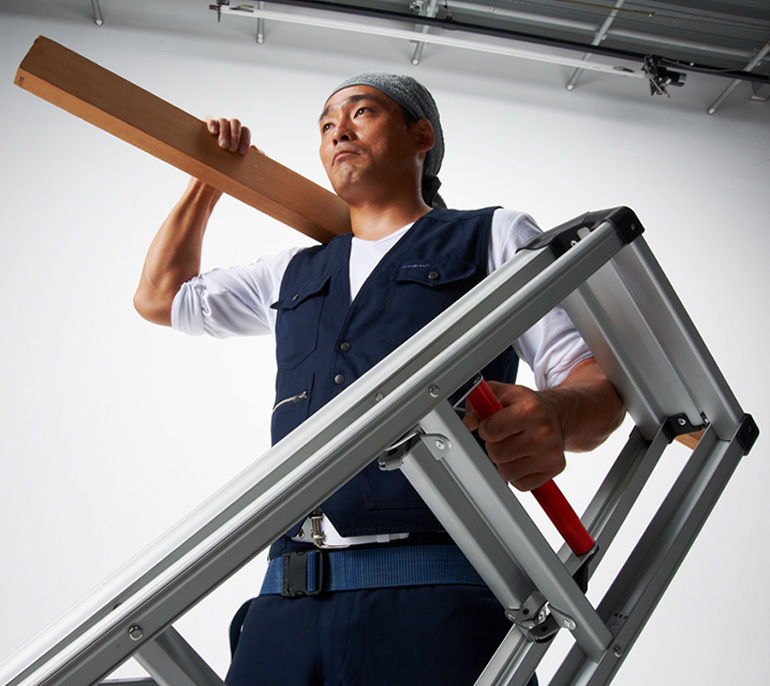
スタンダードを覆す!
開拓者のスピリット
「とにかく軽くて丈夫な脚立がほしいんや!」。きっかけは、職人さんの一言でした。“重い脚立ほど丈夫≒丈夫な脚立ほど重い”というのが、それまでの業界の常識。業界のパイオニアとしての誇りがあるハセガワは、「ないならつくってやろう!」と新商品の開発へと乗り出した。世の中にない製品をつくるには、世の中にはない発想が必要。これまで常識とされていたスタンダードな脚立の概念を打ち破ることで、軽くて丈夫な脚立を誕生させた。そんな、職人を唸らす商品ができあがるまでには、数々の苦労とアイデアがあったのだ。
ありきたりな脚立に
革命を起こす
大胆に発想を転換
最初に行ったのは重さの原因の追究で、材質や部品ごとの重量を徹底的に洗い直した。ユーザーにも調査をした結果、たどり着いた答えは、使用用途を限定させること。これまでの脚立は“はしご兼用脚立”が一般的だったが、10回に1度もはしごを利用しないと判明。“脚立専用の脚立”をつくることにした。
もっと唸らせる
脚立にできるはず!
さらなる工夫をプラス
“脚立専用の脚立”にすることで、耐久性を確保しながら従来の脚立より最大30%の軽量化(当社製品比)に成功。「軽くて丈夫な脚立」が誕生した。さらに、それだけに満足しない開発チームは、新機能もたっぷり搭載。「片手で楽に開閉できるワンタッチバー」「着衣や道具袋が引っかかりにくいフラットな天板」など、ユーザーの声を形にした。
世界に認められ
脚軽からASHIGARUへ
成長し続ける人気シリーズに
人気商品となった「脚軽」は、ブラックタイプと脚部伸縮タイプが加わり「脚軽シリーズ」へと成長。さらにブラックタイプは、全世界の製品を審査対象にした工業製品デザイン賞「iFデザイン賞2014」(ドイツ)に選ばれ、世界的な高評価を受けるように。日本の職人の声から、世界へ。「脚軽」の進化はまだ続いている。
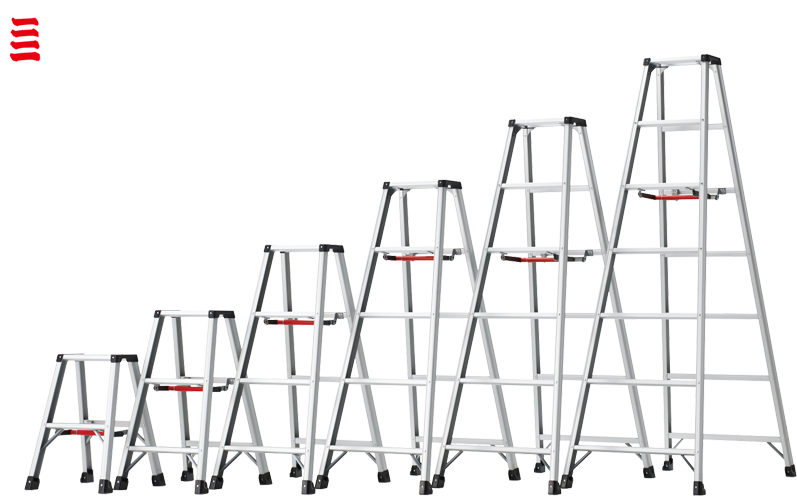
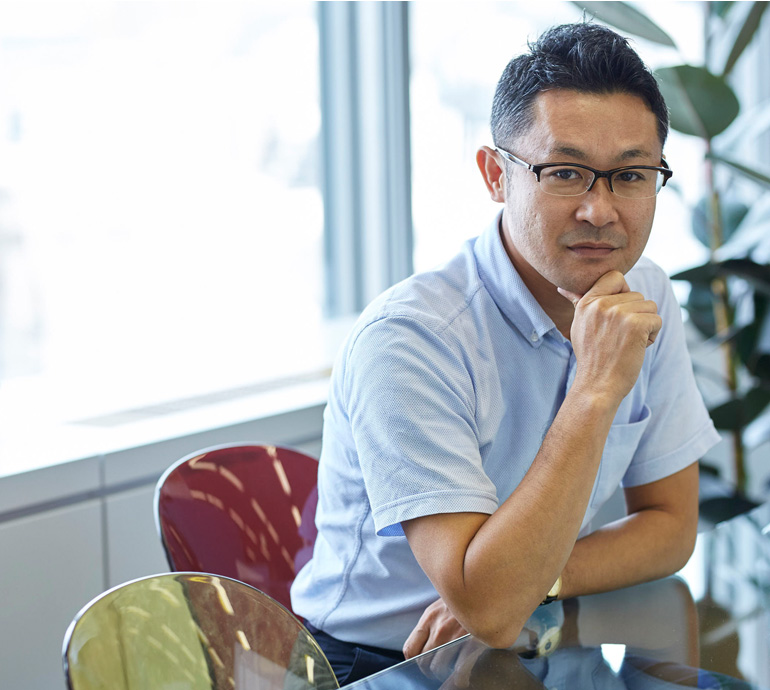
デザインを実現させるための
MADE IN ITALY
座る、昇る、モノを置く、可愛がる。そんな、今までにないコンセプトの踏台として展開している「Purill(プリル)」では、ペットのような存在感を目指して、理屈じゃない可愛さのあるものづくりを行った。とはいえ、ハセガワの製品にとって安心できる品質はマスト。女性でもラクに持ち運びができる「小さくて軽い、軽いのに強い」を備える材質として樹脂に白羽の矢を立て、さらにその独特のフォルムをつくりだすためにイタリアの工場で製造。理想のデザインをカタチにするために妥協をしない、海を越えた誕生秘話をご紹介。
すべては可愛く安全な
デザインのために
イタリアの工場まで奔走
イタリアのデザイン事務所でキャリアを積んだ杉木が手がけたのが、一般ユーザーに向けた、暮らしをちょっと豊かにしてくれる踏台づくり。「感覚的なデザイン」を「プリル」のカタチにするまでに、構想から約1年。可愛らしいフォルムと安全性を両立するために選んだのが、樹脂という素材とイタリアの優れた樹脂成型技術だった。
ときには日本に
こだわらない
柔軟性も必要
イタリアという選択肢
杉木が樹脂の回転成型技術をはじめて知ったのは、イタリア在住当時。金型を回転させながら樹脂を溶かすことで中が空洞になるから、思い通りに成型でき、軽さも備えている。ハセガワの商品開発の中でイタリアの工場へ足を運び、この技術が使えると分かったときには「プリルのデザインをカタチにできる!」と感動したという。
日本と世界を繋ぐ
グッドデザイン
暮らしを彩るアイテムに
部屋にちょこんと置いたときに、ペットのように思わずなでたくなるような可愛い姿と風合い。試行錯誤を重ねたデザインと、それをカタチにする場所と。その両方がかなって、今でも「プリル」はイタリアの工場からやってくる。日本発、MADE IN ITALYの商品は、これから先も、世界中で愛されていくだろう。
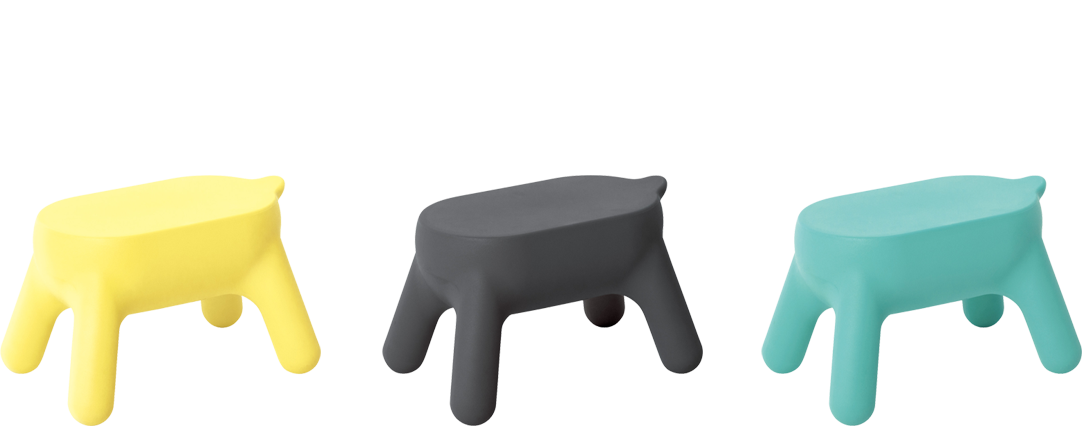
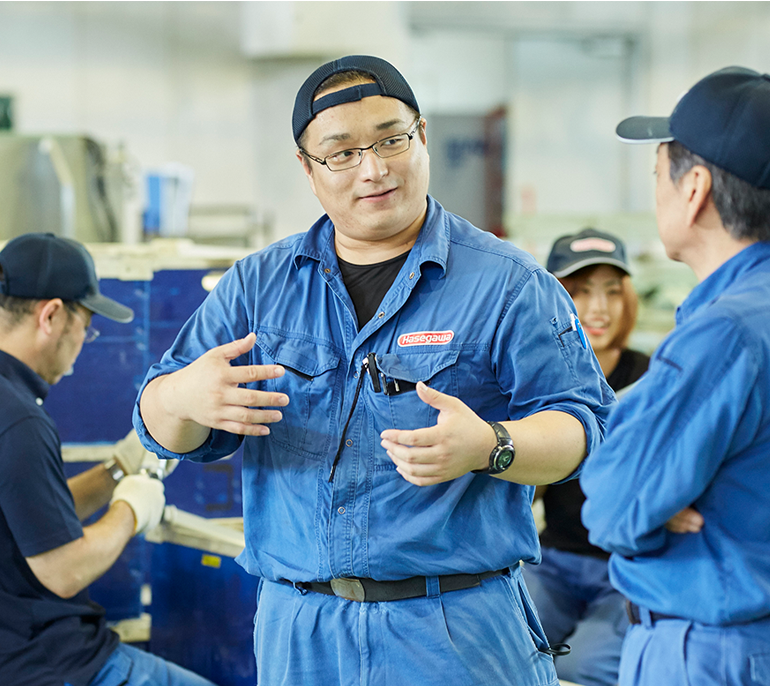
ないならつくる!
それがパイオニアの意地
メーカーであるハセガワがものづくりをするには、製造するための設備が必要。新製品を生み出すということはつまり、新しい製造設備をつくるところからスタートするのだ。そんな“ものづくりの土台”となる製造ラインづくりを手がけているのが、工場の設備を管理する生産技術センター。2017年9月発売の新商品「スカイラダー」では、チームプレーで新構想の製造ライン環境を築き上げた。
今までにない設計の伸縮式はしご「スカイラダー」は、現状の環境では思い通りに製造できない。ならば、製造ラインをつくろう! と動きだしたチャレンジとは。
僕らにとっての
新しいものづくり
が始まる
生産の流れをつくりだす
通常のはしご製造ラインでは部材加工〜組み立て〜完成を数日かけて行うが、「スカイラダー」では「1日に何台かを必ず生産してほしい」という要望が。そのためにどんな機械や金型を使い、どうやって加工するか―。3人は、全体構想・製造ラインの計画・金型と分担して知恵を出し合った。
作業工程の
発想転換がカギに
商品を生み出すために
「スカイラダー」は支柱部分に使う金型が最大24型と、非常に多い。通常通り機械に金型を1回ずつ付け替えていると、とてつもない労力と時間がかかるのだ。そこで導入したのが、あらかじめすべての金型をセットした機械を使う製造ライン。ランプと音声で加工順序を案内してくれるので、間違うリスクも軽減させられる。
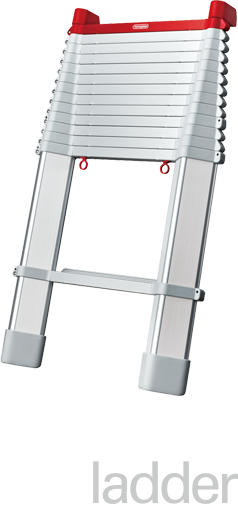